
So best of both worlds for those wanting to experiment running their machines with different Gcode engines.Re: GRBL. Example - G0 G54 G17 G21 G90 G94 M0 M5 M9 T0 S0.0 F500.0 Shows the GRBL version and source code. Displays the active gCode modes in the GRBL parser. Reset GRBL Kill Alarm Lock Run Homing Cycle Lists work coordinate offsets (G54-G59), Predefined positions (G28 & G30), Coordinate offset (G92), Tool Length Offset (TLO) & Probing cycle (PRB).
A better way to securely store and share your business files in the cloud. Axis CNC Machine CNC 3018-PRO Router Kit GRBL Control With Offline Controller 5mm ER11.3 programs for 'grbl control 0.8'. 194.40 (2 used & new offers) 2-in-1 7000 mW CNC 3018 Pro-M CNC Engraving Machine GRBL Control Router Kit 3 Axis PCB Milling Machine Wood Router Engraver with Offline Controller,XYZ Working Area 300 x 180 x 45mm.Being 6-Axis allows for future expansion of the machine.0.7mm Wire Diameter(4-12) mm Out Diameter1000mm Length (Size : 0. Get it as soon as Wed, Sep 15.
Grbl Controller 0.7 Full Size From
These allow for custom made cables to be simply pushed in and connected back to the motors and limit switches. It also has JST connectors for some of the I/O’s that are commonly used on a 3-Axis machine such as the D-500. These I/O’s can be switched to to either configuration by simply setting a jumper or by connecting a single way switch.To view the picture above in more details, you can right click and save the image or click on it and choose view full size from the bottom of the image frame.All the I/O’s have been been broken out to connector blocks and the PCB has legends next to each one. Along with an encoder that makes sure their are no lost steps and great performance.So all we need to do is supply power to each motor and data control lines from our controller board.The controller board itself has a huge number of inputs and outputs to take full advantage of the features found the 6-axis GRBL firmware and the Mach3 interface. The Closed Loop Stepper motors have the driver built on on the motor. Both have power switches at the front of the box.We are supplying it with a branded, genuine MEAN WELL 36V 8.9amp power supply that has a wide range working voltage input of between 88V and 264V AC.As you can see there are no stepper drivers inside the controller box as we now use Closed Loop Stepper motors on all our machines.
Y1 and Y2 are synchronised. The Y Axis also has dual output, so we have Y1 and Y2 which is for gantry systems that use two motors. These are monitored by an ARM processor on the main board which will display which one is triggered by lighting up the indicators at the front of the controller box. These are found on Closed Loop motors. The X, Y1, Y2, Z also have Alarm monitoring connections for the each motor.
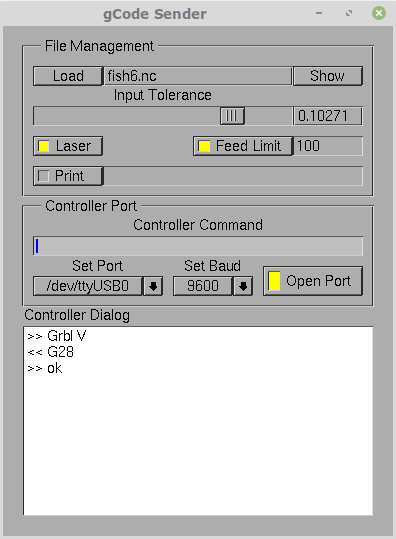

We have tested these and they work well.After you have copied the CNC Design D-500.xml file to your C:\Mach3 folder then launch the Mac Loader Icon.Mach3 should now load and be configured for the D-500 machine.Next Press Reset and press Tab key to bring up the Jog interface.You should now be able to jog the machine around.Grbl is a free, open source, high performance software for controlling the motion of machines that move, that make things, or that make things move, and will run on a straight Arduino. Most new computers these days just have a USB ports.There are USB to Parallel adapters that work well, but must be designed to work with Mach3 such as the USB motion controller UC100. Direct fast output from your PC with no latency like USB.We still use Mach3 to run our workshop machines and tend to pickup old computers from Ebay that still have the printer port. Mach3 configuration.Mach3 has been around for years and very popular.It can be downloaded from Newfangled Solutions on this link, Note that it is not free of charge and will limit you to only a few lines of gcode you can send until you purchase a licence.If choosing to use Mach3 software then you will need to download the configuration file, extract the zip file and copy the CNC Design D-500.xml to your C:\MACH3 folder.The Mach3 Gcode engine software still uses the printer port (Parallel Port) from the computer to send Step, Direction and enable signals, as well as switching spindle and limit inputs. Cutting speed you will specify when creating your Gcode and this will vary depending on the material you want to cut.

